Dongjie always adheres to the principle of "quality proves strength, details win", and has won unanimous praise from new and old customers.
All praise is not easy to get, not the contribution of a single person, but the result of the concerted efforts of the whole team. At the beginning of the establishment of the factory, we knew that we still had shortcomings, so we did our best to improve them. Adhering to this belief, until now, the factory covers an area of 1,000 square meters, has four specialized production workshops, and has more than 100 professionals.
In addition to the factory's high standard requirements for the pre-production process, our quality inspection requirements for products are also constantly improving.
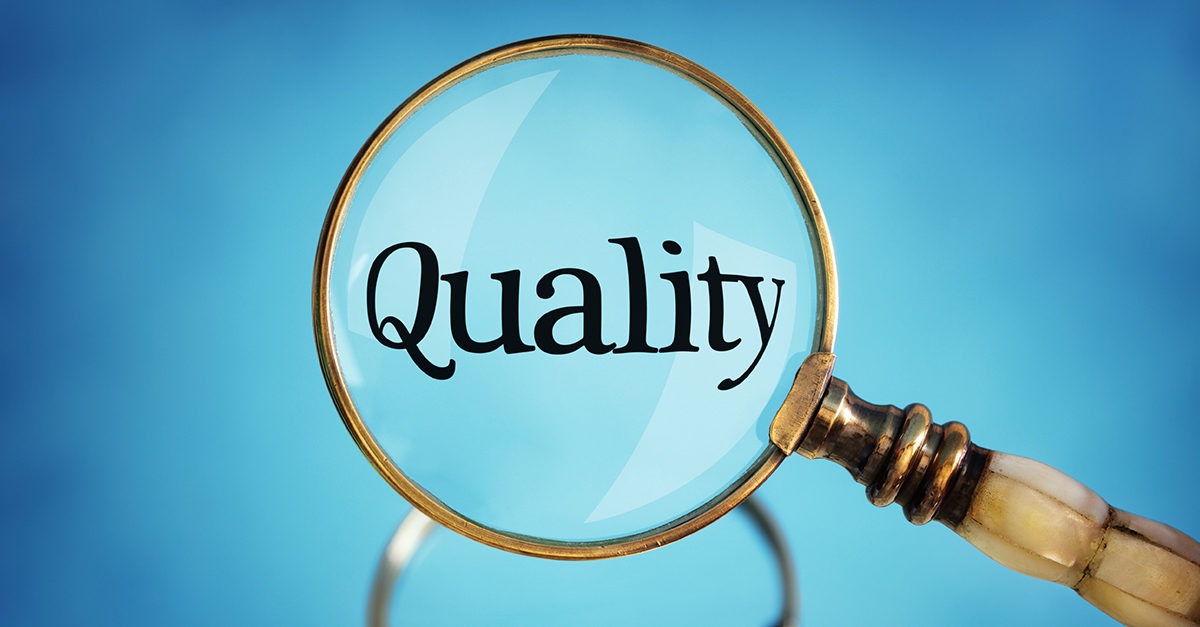
Now Dongjie factory has established a complete product quality inspection process. This process is not only to comply with industry standards and regulations, but also to ensure that our products meet or exceed customer expectations.
Our product quality inspection process includes the following steps:
Incoming Inspection | Upon receipt of raw materials or components, our quality control team inspects them to ensure they meet our specifications and requirements. If any issues are found, we will work with the supplier to resolve them. |
In-Process Inspection | During the manufacturing process, our quality control team conducts regular inspections to find any defects or problems. We use a variety of testing methods including visual inspection, measurement and functional testing. |
Final inspection | After the product is completed, our quality control team will conduct a final inspection to ensure that it meets all specifications and requirements. We use checklists to verify that all components are included, that the product works as expected, and has no defects or issues. |
Performance test | In addition to appearance inspection and function test, we also conduct performance test to ensure that the product can achieve the expected performance under various conditions. This includes durability, reliability and safety testing. |
Packaging and Shipping Inspection | Before shipping the product to the customer, we inspect the packaging to ensure its safety and protect the product during shipping. We also verify that all necessary files and labels are included. |
After-sales feedback | We value customer feedback and encourage customers to share their experience with our products. We use this feedback to continuously improve our product quality and testing processes. |
By following this comprehensive product quality testing process, we are confident in providing high quality products to our customers.
If you have any questions or concerns about our quality testing process, please feel free to contact us.
CONTACT US
Are you still looking for a stable supplier? If you are still troubled by the communication of quality and details, please contact us—Anping Dongjie Wire Mesh.
Focusing on the wire mesh industry for more than 27 years, we have our own factory and professional team to escort your project!
0086-15930870079
NEED HELP?
Don’t hesitate to ask us something. Email us directly at admin@dongjie88.com or call us at 0086-15930870079.
GIVE US A CALL
As a high-quality Chinese manufacturer with more than 27 years of professional production experience, we will recommend the most suitable solution to you one-on-one according to your needs.
AVAILABLE AT 9AM TO 6PM
Post time: Mar-29-2023