What processes are involved in audio speaker covers?
Speaker grilles are usually used on the outside of speakers and speakers to filter dust, decorate and protect the internal structure of the speakers. Currently, they are most commonly used in headphones, car speakers, stereo speakers, etc. The processes used in stainless steel speaker grilles include the following:
1. Stainless steel filter cover stamping process. Stamping process is a widely used processing method. The appearance, grid aperture, graphics and other requirements of the screen produced by the stamping process are not very high. The mold opening cost is relatively expensive and is common in three-dimensional applications. For speakers, the stamping process cannot reach the standard for high-precision thickness.
2. Stainless steel filter cover laser process, the laser process is relatively slow to manufacture, cannot be realized in batch production capacity, and the price is not cheap.
3. Stainless steel filter etching processing technology. The etching process avoids the shortcomings of laser and stamping processing. It uses metal film molds to etch stainless steel with chemical etching liquid through exposure, development, chemical etching and other processes. The etching processing accuracy can pursue a thickness of 0.03MM-2MM, and the processed hole shape, The pattern can be designed arbitrarily. The etched edges of the product have no burrs, no deformation, and do not change the characteristics of the material itself. The etching process of chemical etching is used on the porous aperture to keep the product aperture uniform.
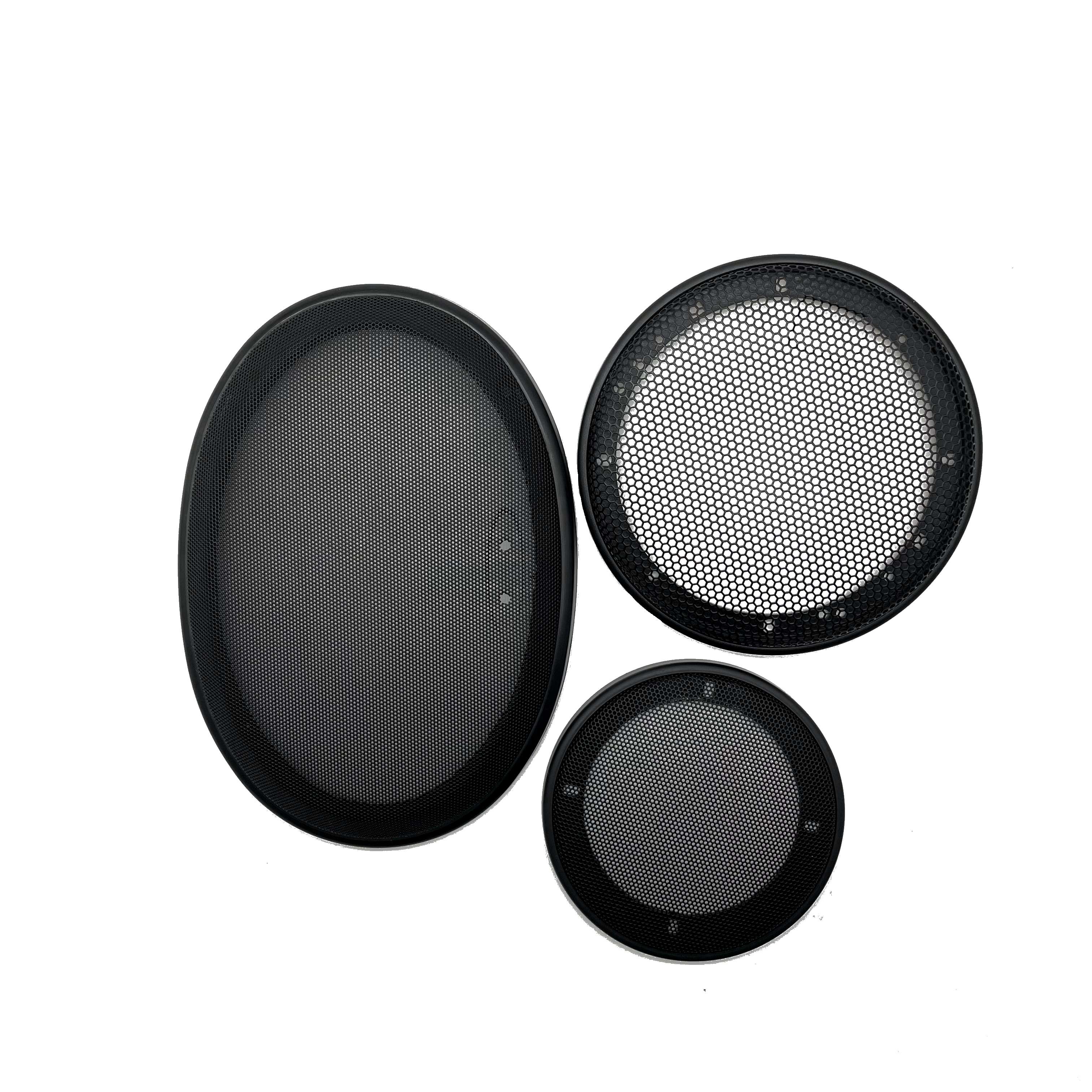
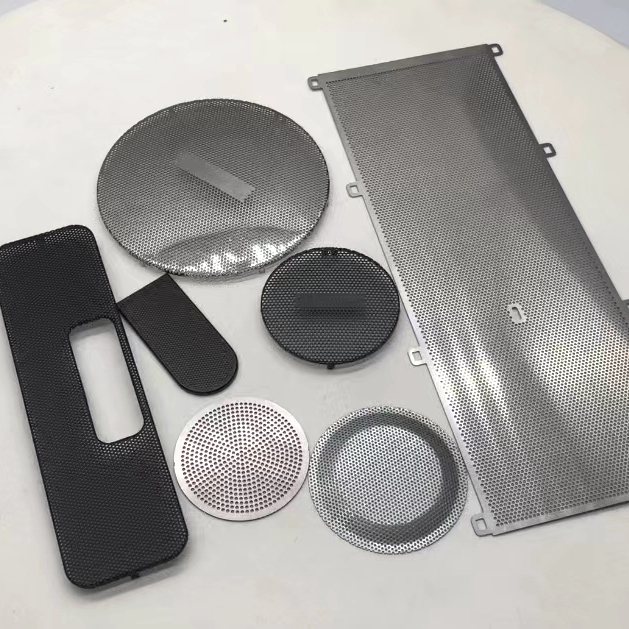
Introduction to several processing methods of audio speaker covers
1. The traditional processing method of metal car speaker mesh is the stamping process. Since the initial metal car speaker mesh has not very strict requirements on appearance, the mesh holes are relatively large, and the spacing is wide. The stamping process requires the production of molds, and the cost of the molds will be high. Relatively high. Generally, no major changes can be made after the mold is made. The advantages of the stamping process are low processing cost and high speed. The disadvantages include the higher mold opening costs mentioned above, the large number of styles, fast updates, and relatively high development costs.
2. Laser processing of car speaker mesh. The advantage of laser processing is that speaker mesh with different meshes and styles can be produced by modifying the drawings. The mesh hole walls are vertical. The disadvantage is that there will be burrs on the edges of laser processing, because high temperatures will be generated during laser processing of metal, and the edges will turn black.
3. Etching and processing of car horn mesh. The etching process is to achieve the processing purpose by corroding the metal with chemical solution. The etched car speaker mesh has uniform mesh, no burrs, no curling, and vertical hole walls. It can process dense and fine mesh. After the drawings are designed, film is used to develop them on the metal plate through exposure. If the drawings need to be modified, only the film needs to be modified to avoid high mold costs. For car horn meshes with many styles and fast updates, etching is used is more appropriate. Compared with stamping, the cost of etching processing will be higher, and the cost is lower than that of laser processing.
Post time: Jan-19-2024